Metal Fabrication Boise is an industry that’s growing fast. The demand is being driven by several factors, including automation and end-market growth.
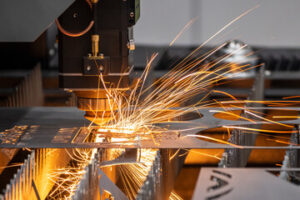
The first step in accurate metal fabrication is cutting the raw material into pieces that are the correct size and shape. The fabricators use tools like mills, shears, lathes, and nibblers to do this.
Metal fabrication is a multi-step process, with each step requiring the right tools and specialized skill. This process enables the creation of customized, high-quality products that are suitable for a variety of applications. It is important to have an idea of what you want your finished product to look like before starting. A fabricator can help with this by creating a CAD prototype. This allows you to visualize the product and make changes if needed.
Several different techniques are used in the manufacturing of metal fabrication parts and structures. These include laser cutting, plasma cutting, and waterjet cutting. Laser cutting provides superior accuracy and can cut through thicker materials with ease. Plasma cutting uses an arc of electricity to cut through metals with little to no heat, preserving the integrity of the material. Waterjet cutting uses a high-pressure jet of water and abrasive materials to cut through thicker metals with speed and precision.
The metal fabrication industry is dependent on a number of raw materials, such as aluminum and steel. These materials can be expensive, and prices are often influenced by global demand and trade policies. Many companies in the industry take steps to control costs by implementing lean processes, using energy-efficient machinery, and recycling scrap metal. Some also use alternative energy sources, such as solar panels or wind turbines.
One of the biggest challenges in metal fabrication is finding skilled workers. Many experienced fabricators are retiring, and there isn’t enough younger talent to replace them. This shortage can lead to longer production times and higher costs. Some companies are working to address this issue by partnering with schools and community colleges to offer apprenticeships and on-the-job training.
It is also important to consider the design of the metal fabrication part or structure when starting a project. Ideally, the design should be simplified as much as possible without sacrificing functionality. This will reduce the number of steps in the process, which will help keep the overall cost down. It is also helpful to consult with a metal fabricator early on to get their input. They can suggest ways to improve the design, lower costs, and prevent unforeseen problems. For example, they can advise that it is better to position holes away from bends, so they don’t distort during bending. They can also recommend the appropriate forming stresses and bending angles for your particular material.
Fabrication
Creating complex metal shapes can be a challenging task for fabricators. Using computers and automated machines, fabricators can cut and shape metal to create precise and accurate pieces. These pieces can be used to build machines, furniture or even skyscrapers. However, this technology is not without its drawbacks.
Automation can lead to a loss of jobs in the metal fabrication industry. Many experienced metal fabricators are retiring, and there aren’t enough new workers to replace them. As a result, the US metal fabrication industry faces stiff competition from countries with lower labor costs. However, some fabricators are finding ways to stay competitive by focusing on their strengths. They are also embracing advanced technologies and investing in their facilities.
The key to success in the metal fabrication industry is the ability to produce high-quality, durable products that meet specific customer requirements. For example, a manufacturer may need to produce one or more prototypes before beginning production. In addition, they will need to ensure the design of a product is practical and cost-effective. The fabrication process also includes a quality control and inspection process.
Specialized companies in the metal fabrication industry offer a variety of services, including customization, diverse material options, precision manufacturing, value-added service and quick turnaround times. These advantages help them meet unique customer needs and provide a competitive advantage.
A specialized metal fabricator can also provide design assistance, prototyping and high welding quality. In addition, they can millwright, cut, form and finish parts. A one-stop solution saves time and money, and it allows for consistency throughout the fabrication process.
Choosing the right metal fabricator is an important decision that requires careful consideration. Look for a company that has experience in your industry, a good track record and a strong work ethic. A reputable company will also have a team of qualified professionals and an excellent safety record.
Another consideration is the location of a metal fabrication shop. A good location should be close to the customers, have easy access to transportation and avoid areas with poor weather conditions. Some factors to consider include utility needs, the availability of skilled labor and a business climate that supports growth.
Assembly
Once the fabrication process is complete, the individual components must be assembled into a whole. This can be done by welding or binding with adhesives. The choice of assembly method depends on the final product’s purpose, durability and function. For example, a machine that requires a fastener for maintenance purposes would be better suited to adhesive bonding. In other cases, it is necessary to weld metal parts together. This could be done using a variety of welding processes such as GMAW or GTAW, depending on the application.
Assembling a metal fabrication project requires multiple steps that are completed by different teams in parallel. This means that it is essential to work with a partner that offers a complete suite of services. A one-stop solution streamlines your project management and ensures that the highest quality standards are maintained throughout the process.
A full-service partner should offer a wide range of cutting, forming, finishing and millwrighting capabilities. It should also have access to state-of-the-art equipment such as CNC laser cutters, machining centers and press brakes. A good partner will also have a team of skilled and experienced metal fabricators who can handle various fabrication tasks.
The first step in the metal fabrication process is to cut the raw materials into pieces of the desired size. This may involve shearing, sawing, chopping or torch cutting. Afterward, the edges are deburred to remove any sharp or rough edges. A bending process is then used to shape the metal into the desired form. The bending process can use mechanical shearing, guillotine shears or power bending equipment.
Other forming techniques include rolling, spinning and drawing. Roll forming shapes sheet metal by passing it through a series of roller dies. Spinning is another forming technique that uses a rotating shaft to shape the material. This method produces a variety of cylindrical products, including hubcaps and cookware.
Welding and brazing are commonly used joining methods in the metal fabrication industry. These methods join parts with a strong, durable and permanent joint. They are ideal for applications that require a lot of pressure. Other joining methods include rivets, screws and adhesive bonding.
Installation
Behind the most advanced skyscrapers, high-speed trains and cutting-edge machinery lie a myriad of carefully and precisely assembled fabricated metal components. Fabricators are responsible for bringing to life the visions of architects, designers and engineers by turning raw materials into bespoke constructions that exemplify the best in design and functionality.
In the field of architecture, fabricated metal components make up the structural bones of buildings, bridges and tunnels. From creating supports and beams to constructing the façade of buildings, these components must be engineered for both strength and aesthetics, while maintaining safety and durability.
The use of welded and clad structures also plays an essential role in the transportation sector, with fabricated metals used to create vehicle components like frames, engines and fuel tanks. Metallurgical fabrication is also used in the energy industry, from oil and gas production to wind power and solar energy fabrication.
When it comes to commercial and retail spaces, metal fabrication often takes on decorative and ornamental designs. These may include awnings, gates and fences or furniture, blending aesthetics with practicality. Fabricators also produce storage and process tanks for industries like food and beverage or pharmaceuticals, optimizing storage capacity and hygiene standards.
In the world of art and interior design, fabricated metals can be used to create sculptural installations or gallery pieces. These are often commissioned and based on a specific theme or idea, making each piece unique. Metal fabrication is also a common material for furniture, providing strength and design flexibility.
Regardless of the scope of the project, any metal fabrication process starts with a careful study of the needs and goals of the end product. This helps the fabricator determine which tools and processes are required to achieve the desired results. For example, metal alloys are chosen based on their properties such as durability and corrosion resistance. A suitable machining and cutting method is then chosen, with lasers, waterjets, presses and brake machines transforming raw materials into the desired forms. Welding and fusion techniques are then used to fuse the metal together, and finishing methods such as deburring, grinding, polishing or coatings give the fabricated object its finish.